Fabrication
Fabrication is the act of taking raw stock material and turning it into a part for use in an assembly process. There are many different types of fabrication processes. The most common are
- Cutting
- Folding
- Machining
- Punching
- Shearing
- Stamping
- Welding
- Additive Manufacturing
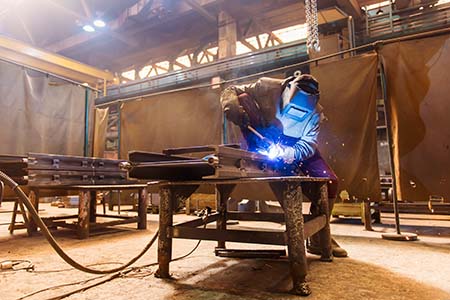
Let’s look at the types of fabrication processes in greater detail here:
- Cutting. There are many ways to cut nowadays. The old standby is the saw. Others now include plasma torches, water jets, and lasers. There is a wide range of complexity and price, with some machines costing in the millions.
- Some parts need to be bent. The most common method is a press brake. It has a set of dies that pinches the metal to form a crease. This operation can only be performed in very specific cases due to the range of movement of the part during the bending process and the possible shape of the dies. Designing for Lean manufacturing, though, can help prevent complex shapes that slow down production. Sometimes using two different types of fabrication processes or two different pieces fastened together work better than one complicated piece.
- This is the process of removing metal from a piece of material. It might be done on a lathe, where the material rotates against a cutting tool, or in some other cutting machine where a rotating tool is moved in a variety of ways against a stationary piece. Drills fall into this latter category. The range of motion of the cutting head is defined by the number of axes (i.e. a 3-axis machine).
- Punching is the act of a punch and a die forming a scissor effect on a piece of metal to make a hole in it. Obviously, the punch and die must be the same shape and size of the desired hole. In some cases, the main piece of material is kept, as in when holes are added for fasteners. In other cases, the piece that is removed is the desired product-this is called “blanking”.
- Shearing is the process of making a long cut on a piece of metal. It is, in effect, just like the action of one of those paper cutters with the long chop-handle. This is done on sheet metal.
- Stamping is very similar to punching, except the material is not cut. The die is shaped to make a raised portion of material rather than penetrating.
- Welding is the act of joining two pieces of metal together. A variety of types of welding exist for use in different applications and for the range of metals used in manufacturing.
- Additive Manufacturing. This is a relatively new technology. In effect, a machine layers material to form a part. It functions similarly to a three-dimensional printer that produces components in plastic (or other similar materials) but can be done at much larger scale and with more varied materials than typical printers. They can even be big enough to produce entire houses. The geometry of the component produced can be limited due to the effect of gravity on the fluid materials before they become rigid.
There are many other types of fabrication processes that are less common than the ones in the list above. There are also constantly new types of fabrication methods being developed (such as additive manufacturing listed above).
Fabrication processes are particularly well matched to Lean. The motion of operators, their interaction with machines, and the need to manage inventory are all right in Lean’s power alley.
Fabrication processes are especially compatible with implementing jidoka (autonomation) and hanedashi devices (autoejectors). Both of those devices are prerequisites of the chaku-chaku line (load-load).
But there is one area where Lean can struggle. Some extremely large machines are well matched to the products they are making. But far too many big machines with too long of a changeover time drive up inventory and promote overproduction. It is best to “right-size” machines and put them into work cells if possible. That helps create flow.
The biggest impediment to making flow in a fabrication shop is the preponderance of large, multi-function machines that take a long time to change between parts. This drives up the lot size, creating inventory. It also means that a machine may be used to produce many different components for several product lines. Deciding where to put it is a challenge. If you include it in flow of one line, even the biggest line, it would be a problem for all the other lines.
The task in this case is first and foremost to reduce the changeover time so that the machine does not run large lots. At that point, you can keep reducing the amount of inventory that the machine creates. The second task is to get away from buying large, expensive machines when smaller, dedicated ones will suffice. In many cases, a small machine can be automated with jidoka and hanedashi to make their efficiency rival that of large CNC machines.
One challenge with linking fabrication and assembly processes tends to be the painting process. In many cases, parts leave the fabrication shop to go out for painting or go right to an in-house paint center. In either case, the flow is disrupted, and the delays cause more inventory. Again, use the CI tools at your disposal to minimize this impact—reduce cure time, reduce the changeover, make smaller batches, go to smaller, dedicated paint booths. Do what you can to keep coming closer to flow.
Continuous Improvement in Fabrication
Fabrication processes are generally target-rich environments for continuous improvement. There are great chances for visual management and 5S to make processes run more smoothly. There are immense opportunities to reduce setup time to help lower lot sizes. Kanban helps with knowing what to make—especially on the extremely large machines. Right-sizing machines can help make flow better—smaller machines fit in smaller spaces that can be set up as dedicated lines for higher volume products.
Fabrication processes tend to have another great opportunity in continuous improvement—the working environment. “Fab” processes tend to be hot and grimy. Small metal shavings are everywhere, as are coolants and lubricants. Parts are often heavy. Smoke and debris are in the air.
To top it off, safety concerns abound. Machines are unforgiving. They are designed to work with metal—hands and other body parts don’t even slow them down.
Machines are extremely loud. Unless you have experienced it, is it hard to imagine…
Extended Content for this Section is available at academy.Velaction.com
Take a close look at your fabrication processes and identify all the issues that pose safety risks or that are generally frustrating to your team. Rank order the problems. (Note: The safety issues should be at the top of the list.)
Begin applying your Lean toolkit to removing these issues. It might sound a bit like a haphazard approach, but the goal is one that aligns with the big picture. You are attempting to build support for the problem-solving processes that continuous improvement demands. Once team members see that there is some benefit to them, they will be more willing to take on the bigger projects that improve flow.
Those types of changes—running smaller lots and arranging by product line rather than function—generate much more resistance. Having a solid track record of success makes people more accepting of change.
13 Comments
Alice Carroll · February 4, 2021 at 7:29 pm
You made a good point that custom plastic fabrication often comes with 3D printing technology nowadays. I think it will opt for a service like that when prototyping some products that I’d like to sell in my own novelty store someday. I’ve been trying to design toys these past few years but I’m not very good at producing them in a practical way so it’s best to let experts handle it.
Jeff Hajek · February 5, 2021 at 8:34 pm
It’s not just plastic for 3D printing. Metal printers are getting better all the time, and in the video I even talk a bit about giant 3D printers that can print houses. There is even a printer that has a UV light that hardens materials instantly which allows it to span gaps. Technology is charging ahead.
Abdul Salam AL barwani · January 27, 2021 at 10:55 pm
Am taking over as general manager of the fabrication campanie and I want to improve the quality, standards and safety of the employees by using new technologies, so I can axcellerarate the production line.
Jeff Hajek · January 28, 2021 at 1:52 pm
Great goals. You’ve come to the right place for information on that. I recommend https://academy.velaction.com/continuous-improvement-video-series for great videos and downloads, or https://store.velaction.com/products/5s-and-visual-controls-lean-exercise for training packages to get people using more Lean tools.
Good Luck.
Chris Pederson · December 29, 2020 at 8:22 am
I’m glad to see there is continuous improvement in fabrication. Too many people overlook this and just want the same stuff. Newer materials and designs are better and more efficient.
Jeff Hajek · December 29, 2020 at 9:31 am
I think many people equate continuous improvement with Lean, and Lean with assembly processes. There is so much opportunity to improve fabrication operations. Plus, as you mentioned, new materials and innovative design methods go a long way towards making fabrication easier.
Thanks for the comment.
Ron Booker · April 22, 2020 at 11:46 am
I believe that the most important factor to consider when hiring a metal fabrication company is their experience, as stated here. My dad needs to get some shearing and punching work done to finish his construction job, so he asked me to finds him a welder in the area. I will keep in mind the tips you provided so I can narrows down my options and hire the right company for the job.
Thomas Clarence · April 21, 2020 at 11:30 am
I found it interesting when you explained that machining is the process of removing metal from a material. If I were to guess, this process would probably be very useful in sheet metal fabrication. It would be interesting to learn more about the types of products that are created in fabrication.
Daphne Gilpin · February 13, 2020 at 8:00 am
It was interesting when you talked about how shearing metal is the action of making a long cut on a piece of sheet metal. My brother needs to find a good industrial fabrication service to manufacture the steel frame for the new warehouse he’s constructing just outside the city. The info you shared here should prepare him to talk with potential fabrication services, so I’ll be sure to pass it along!
Jeff Hajek · February 22, 2020 at 9:11 pm
Tell your brother good luck!
Angela Waterford · December 10, 2019 at 12:59 pm
My professor told me to research on the different methods of steel fabrication that are being used by fabrication companies these days since he told me that I’m going to be the one who will present that lecture for my classmates next week. I didn’t know that one of the most common tools for cutting steel nowadays is the use of water jets. Maybe I can ask someone who does this for a living and get more in-depth information about how the process works so I can report that in front of the classroom.
Jeff Hajek · December 15, 2019 at 10:12 am
I think it is a great idea to find someone who can help. You might even be able to find a local company who would give you a tour. I’d try linkedin to see if there are any close connections to a local manufacturing company.
Eileen Benson · November 18, 2019 at 8:09 am
It was interesting when you explained that during the punching process, the punch and die are required to be the same size as the hole being made. The company I work started designing a new product last month, and we’re currently in the process of looking for a metal fabrication service to manufacture some needed parts. Reading your article helped me feel more prepared to talk with potential metal fabrication companies about the services they offer!