Cycle Time
In nearly all continuous improvement projects, it is important to know how long work takes to accomplish, known as the cycle time of the process. So, what is cycle time?
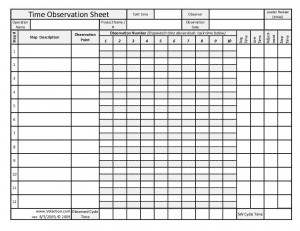
Track your cycle times with our free time observation sheet (Click image to get it.)
Lean defines cycle time as the time it takes to do a process. It includes the time from when an operator starts a process until the work is ready to be passed on. This cycle time definition is rather simplistic, though, as there are several elements that can cloud the issue. Batching makes it hard to determine cycle time, as does waiting. On linked assembly lines, there is often waiting at the end of a line shift. That waiting is typically not considered part of the cycle time but waiting within the work sequence is generally included. Put simply, cycle time is the minimum time a stopwatch would have to run to produce a good unit of work.
In addition to the vanilla version of cycle time, you may hear several other variations which lead to further confusion: operator cycle times, machine cycle times, or automatic machine times.
The purpose of knowing cycle time is to establish staffing, do demand planning, and provide the basis for continuous improvement.
Lean, and all continuous improvement philosophies, place a tremendous emphasis on time. After all, it is a component of one of the key operational metrics that many companies use to determine performance: productivity.[1]
Many people define cycle time in slightly different ways. One definition you might hear is that cycle time is the time between the completion of one unit, and the completion of the next unit. There is a problem with that definition of cycle time, though. Sometimes an operator finishes her work early, and has to wait to start the next one.
In practice, that definition means that cycle time will always equal the time between shifts of an assembly line (most likely set equal to the takt time). Plus, all the cycle times would be identical on that line. Those who use this definition, though, often break it into two smaller components—processing time (the time an operator is actually working) and wait time. So, under this definition, cycle time looks like this:
Cycle time = processing time + wait time
The more common definition of cycle time is the equivalent of processing time in the equation above—the start-to-finish time of an individual unit. Note that even this definition of cycle time creates some opportunity for confusion. Often there are bits of waiting within the process. Perhaps a person has to wait 20 seconds for some glue to dry or for 16 seconds while a machine tests a circuit. Most people differentiate between the waiting embedded within a process and the waiting to pass the work on once the work is complete. Ironically, that end of cycle waiting is more prevalent in Lean organizations where operators can’t pass work on until there is a pull signal, as opposed to batch and queue operations where an operator just keeps working whenever there is material available.
We recommend using the elapsed start to finish time for cycle time. This would include the waiting within the process, but not at the end. The truth, though, is that as long as you understand the concepts, the choice you make as to definition is less important than the fact that measuring processes and understanding the time content leads to improvements. Just makes sure you know the usage at your company to prevent misunderstandings.
Real(ish) World Cycle Time
Let’s talk about how this works in real life. There is a YouTube video that shows a clip of the old “I Love Lucy” show. It is the one where she is working on the production line in a chocolate factory.
In the episode, you can see in an amusing way, how cycle time and takt time interact. Lucy and Ethel are working in a chocolate factory, and have to wrap chocolates moving along a conveyor in front of them. Initially, the pace is rather slow. Presumably, the conveyor is running at the speed that matches takt time—it is set so that a chocolate passes Lucy every three seconds.[2]
If she was working alone, she’d have to be able to wrap each piece within three seconds to keep up. Since Ethel was with her, she only has to do every other piece, so she’s got six seconds.[3] If it takes her three seconds, she’s got a three second cycle time (or processing time), and three seconds of wait time.
To get a few laughs, eventually the line speeds up. In reality, this happens when customer demand rises. At some point, Lucy realizes that she can’t keep up, and chocolate starts flying. In your workplace, the effect is more subtle, but the same thing happens. When the pace is faster than the cycle time, workers can’t keep up with demand.
On the flip side, if the cycle time is much lower than takt time, the operator will be standing around. Not a very efficient situation. The goal is to balance cycle time to takt time.
[1] Productivity can be measured many ways. One of the most common is units per labor hour.
[2] There’s some math involved here that involves the spacing between the chocolates and the speed of the conveyor to determine how often a piece of candy passes in front of Lucy.
[3] Sorry. More math here…To figure out how many people you need for a production task, you divide the total cycle time of all tasks by the takt time. It doesn’t matter whether people do tasks in sequence (like on a true assembly line) or they all do a complete unit, like the Lucy example. The only catch is that math assumes that the work is perfectly balanced (everyone gets the exact same amount of work). It never is, so there always more people than the equation says there should be.
Warnings About Using Cycle Time:
- Using the wrong term creates confusion. You say one thing, and others hear something else. Make sure you know the accepted definitions of these terms in your company. Regardless of the definition that you use, make sure you understand how people and machines interact, and how their current processes stack up against the takt
- This entry focuses on the time it takes a person to do a job. Many times, a worker will be using a machine. Make sure you understand how operator cycle time relates to machine time (also called machine cycle time), or to automatic machine cycle time. A Standard Work Combination Sheet (SWCS) shows this interaction.
- Cycle time should be measured for a process, not a person. Obviously, a fast person will post better times than a slow one or an untrained one. Solid, repeatable processes and good training, though, will minimize this variation. Regardless, time an average person at a normal pace when measuring cycle time. It will cut down on the number of disputes about whether the time is reasonable.
- Takt time remains constant unit to unit. If cycle time was measured on each cycle, there would be some variation. The more variation, the less stable the process is, and the more wasteful it is. Get rid of variation, and average cycle time will come down.
- Before attempting line balancing, focus on cycle time reduction. Bring the cycle time down so you don’t just move a poor process from one location to another.
- Never trust an even number for a cycle time on a Standard Work Combination Sheet. There is only a 1 in 60 chance that a time ends in :00. (There is only a 1 in 15 chance that it ends at any of the four favorite SWAGs—:00, :15, :30, or :45) It indicates that whoever recorded the times logged estimates. That means that nobody actually observed the work when recording the SWCS, which means that there is probably a lot of waste in the process.
- Standard Work Sheets document cycle times. Periodically review the sheet to make sure that the times that are recorded match reality. If they don’t there is a high likelihood that the process is out of date, raising the chance of quality
- Cycle time gets confusing when batching is involved. Lean tries to get rid of batching, but it will likely still occur to some degree, especially in fabrication areas on CNC machines. To find the cycle time of an individual part, you end up doing what is called amortizing, or allocating out the overhead time. For example, the setup time of a machine is divided up between all the parts in that run. Or, in an assembly area, a person might apply glue to parts and then shine an infrared light on several at once to set the glue. Conventional wisdom says bigger batches lower the cycle time per unit. This is, of course, contrary to good Lean principles. Resist the urge to increase batch size to lower cycle time. Instead, focus on flow, setup reduction, and the like.
It takes a long time to get past the idea that cycle time is not a measure of you, but rather of your process. Most people see a stopwatch and immediately get nervous or annoyed that they are being evaluated. The best way to get past this hang-up is to get used to being measured. Volunteer to be the one to get timed for Standard Work as often as you can.
You will also have to get used to the idea that no cycle time is ever low enough. Just when you think you’ve finally settled on how long a task should take, one of two things will happen. First, someone will have an idea, and they will put it in place, lowering the cycle time. This is more of a mental block than a real problem. If a process takes seven minutes, and someone comes up with a good way to do it in three, what’s the problem? The problem is that those four minutes get filled, so it feels like more work is getting dumped on you. Step back, though, and look at the quantity of time, not the number of tasks. The catch—if more work is added before the cycle times come down, you are doing more work.
The second thing that might happen is that your boss gives you an improvement target. This often happens when she knows demand is picking up and has a new target takt time to hit. That will result in a push to improve a process and reduce the cycle time. Until you get comfortable with the continuous improvement process, you will struggle with this. But think of it like visiting a new city. If you know the general rules of travel—how to get through an airport, read a map, and rent a car—you’ll be able to have some fun. You wouldn’t avoid travel because you don’t know the exact layout at your destination’s airport. In the same way, once you get a few improvement successes under your belt, the goal of reducing cycle time won’t feel like such a burden.
Exclusive Content for this Section is available at academy.Velaction.com
Key Points to Using Cycle Time:
- Cycle time is the length of time—start to finish—to complete a process. It should include the waiting steps that are part of the process.
- Some definitions of cycle time vary—make sure that you use the term the same way your company does.
- Cycle time should be balanced to takt time to create an efficient workspace that can meet customer demand.
- Strong math skills are needed to progress in Lean.
Steps to Get Started Using Cycle Time:
- Establish an accepted definition of cycle time. It is important that everyone in the company calls it by the same thing, or there will be confusion.
- Identify a fairly stable process and establish Standard Work for it. That will require documenting the cycle time.
- Identify potential problems where the cycle time of a process seems off. Look for parts of the process where the cycle time seems too long (i.e. lots of waiting), where there is excessive variation, and, of course, where there are clear opportunities to improve.
- Do daily improvement or schedule a project to make the improvements identified in step 3.
- Go back to step 3 and repeat.
Note about timing your process: For the shop floor, use the Time Observation Sheet. In the office, use the Office Process Recording Sheet. You will likely learn a great deal about your operation simply by watching and timing. If your cycle times fluctuate wildly from one observation to the next, you should start your improvement process by focusing on variation reduction.
Cycle time is a major component of Standard Work module, part of our Velaction Training System. Included in this module is a video, PowerPoint presentation, Student Guide, and a 96-page Lean Tutorial, Structuring Standard Work: A Leader’s Guide to Developing Standard Work that Works.
Velaction offers a Time Observation Sheet that is useful for tracking cycle times when creating Standard Work.
0 Comments