Don’t Go Crazy with Your 5S
I often see people focusing on technical aspects of 5S, rather than the purpose of what 5S is all about. Remember, 5S is intended to create a more productive, effective workspace.
Some common errors include:
- Defining a location for a fixed object. Some people like to outline everything, but I simply don’t see the need to run a piece of tape along the edge of a stationary machine just so it is labeled.
- Labeling the obvious. No need to put a tag on an item stating what it is, unless there is a cause for confusion. Label the location, of course, but most people can correctly identify a stapler 8 out of 10 times.
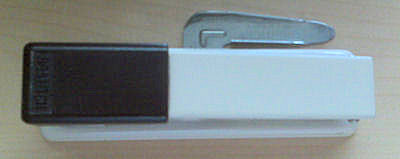
Now what is this thing again?
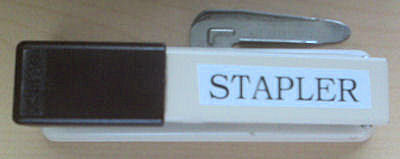
Oh yeah. Now I remember.
- Going overboard on red tagging. Clearing the unused items out of an area is good. Getting rid of necessary items is not. Use a red tag system to make sure spring cleaning doesn’t shut down a process.
- Forgetting the human element. 5S should make things easier and better, not harder. Don’t forget that people have to live with the 5S decisions you make. Good 5S makes people WANT to follow it.
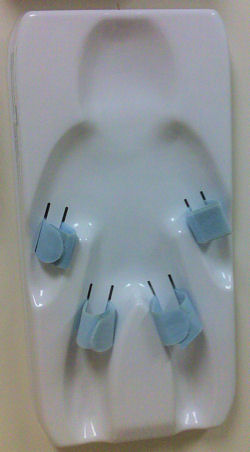
5S Taken WAY Too Far…
So, what examples have you seen of 5S taken a bit too far? I’d love to hear about extreme cases of 5S that you’ve seen in your Lean travels.
6 Comments
Mark Graban · September 11, 2010 at 9:54 am
I’ll link to your post from there too, but did you see the “Office 5S Gone Bad” video that I made?
http://www.leanblog.org/office5S
Jeff Hajek · September 11, 2010 at 9:59 am
Yeah–I saw it and smiled the whole time. I’ve heard most of that commentary before in real life (unfortunately), just not all in one go like that.
You’ve got to have a sense of humor to manage all the change that Lean brings.
Tracy · September 10, 2010 at 6:22 pm
We have brgun our Lean journey and have had some of our team go way overboard as well. They not only labeles everything on the desk but also labeled the chair seat with (butt)! lol
Jeff Hajek · September 10, 2010 at 7:12 pm
Tracy,
It sounds like you have a fun team. I like having some levity like that in the workplace. I just worry a little about the team when there is a push to get everything labeled instead of making jobs easier to do.
By the way, how is your team responding to the new ways of doing things?
Jeff
Val · September 10, 2010 at 9:54 am
Slightly confused as to the last picture on over 5s-ing, what is this, is it a doll case or a baby changing bench? Prehaps this is in need of more 5S not less 🙂
Jeff Hajek · September 10, 2010 at 10:00 am
Val,
It is an infant restraint in the room where I get allergy injections. It just got me thinking about extreme 5S when I saw it. I’ve been doing continuous improvement for so long now, I see it everywhere I go…
Thanks for commenting.
Jeff