Implementing Lean in 3 (Not So) Easy Steps
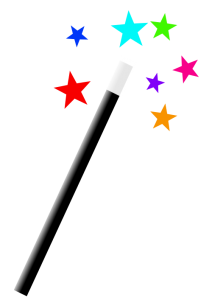
There’s No Magic Wand for Implementing Lean
I am often asked about what can make implementing Lean easier, or how to do it quicker. Unfortunately, implementing Lean takes a lot of effort. It requires a lot of expertise, experience, and a wide array of skills to make it successful. There are no magic wands, special beans, or secret scrolls passed down from the tribal elders. But there are a few actions that leaders can take that will help start their Lean efforts off on the right foot.
The Foundation of Implementing Lean
- Believe. Leaders should set aggressive targets and commit themselves and their teams to hitting them. With lofty targets that stretch people’s comfort zone, they will seek out ways to reach them—especially if their personal success is tied to the organization’s success. And if they find a better non-Lean way to meet those goals, good for them. The goal is not to be Lean. It is to get better.
- Know. Leaders should get rid of words like hope (as in “We hope that this change will solve the problem”), think (as in “We think the problem is with the…”), might, could, or other words that show guesswork in problem solving. Leaders should learn to identify the wishy-washy indicator words, and then shift to acting with real information. A long time ago, I had a boss who used to say, “Hope is not a method.” That concept stuck with me.
- Predict. Leaders should start every day with a prediction about what the team will accomplish. It does two things. First, it makes them think about the plan. To predict that 37 orders will be processed today, they have to understand demand, pace, staffing, and a bunch of other factors. That means scrutinizing the process, which makes problems leap out. The second thing predicting does is makes deviations obvious. And since nobody likes being wrong day after day after day, most people try to do something about it.
Doing those three things won’t make a team Lean. But they will lay the foundation. Most people immediately want to jump into learning the Lean tools when they start implementing Lean. In truth, learning the tools is the easy part. The hard part is building the desire to actually put the tools to use.
(Note: The magic wand image is public domain and was obtained courtesy of Wikimedia Commons).
0 Comments