Mistake Proofing: Temporary Speed Bumps and Schools Zones
In the last few months, I’ve seen several speed traps set up in schools zones where multiple police officers line up and systematically pull over a steady stream of drivers.
Now, I’m not in the car with those drivers, but I would bet that most of them aren’t intentionally trying to put children at risk. In most cases, I would bet that the excessive speed is a result of inattentiveness to their surroundings.
Given the number of drivers that were pulled over, it seems pretty clear that the signs and flashing lights were not working all that well.
The problem is that ticketing speeding drivers is treating a symptom, not the underlying root cause.
In the workplace, it is common to see a similarly ineffective band-aid when a problem is identified. It usually goes something like this:
- Management identifies a process doesn’t provide consistent results.
- Management throws attention at it and reminds employees there is a problem.
- The problem subsides.
- Management moves back to their other responsibilities.
- The problem comes back.
The simple truth is that scrutiny only improves a poor process while the scrutiny is present.
The only true way to prevent problems is to improve the process itself, often with the use of a mistake proofing device, or poka yoke.
In the school zone example, mistake proofing means ensuring that drivers can’t speed. The sign doesn’t make drivers slow down, but something like using temporary speed bumps out on the road when children are present, would reduce the number of errors—in this case, overly fast drivers.
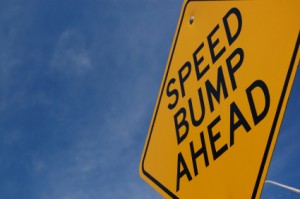
Speed Bumps: Mistake Proofing in School Zones
In a Lean environment, it may be a little more complicated than throwing a piece of plastic out on a road a few times a day, but it is well worth the effort of mistake proofing in order to solve a problem and prevent the waste of rework.
0 Comments