PDCA Cycle
The PDCA cycle is a structured problem-solving approach. It is also known as the Deming cycle, after Dr. W. Edwards Deming, the man credited with popularizing the Plan-Do-Check-Act cycle.
The 4 Steps of the PDCA Cycle include:
- The plan step of the PDCA cycle entails setting objectives and gathering the information needed to make improvements.
- In this step, the problem solver implements the plan. They will often do experiments or pilot projects as well.
- Problem solving requires confirmation that the change actually improved things. Problem solvers do this in the “Check” step of the PDCA cycle.
- After checking, a problem solver must act on the information. It could be stabilizing the change, if things are going well, or repeating the PDCA cycle if there was still an unresolved problem.
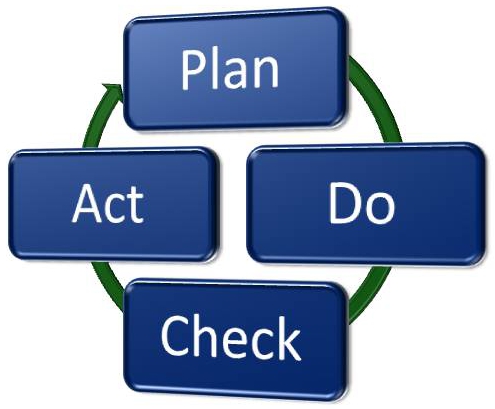
The PDCA Cycle
The PDCA cycle is frequently associated with daily management. Leaders in Lean organizations have a responsibility to make things better. This tool helps them use a structured approach to make decisions when solving problems.
The Definition of a Problem
The basic definition of a problem is that there is a gap between an expectation and reality. The gap can be formed in one of two main ways.
- There is a decline in performance and the expectation stays the same.
- The expectation rises even though there is no change in performance. This shift in the target can come from an internal decision or as a reaction to external changes a competitor is making.
Why People Fail at Problem-Solving
There are many reasons why people fall short in their problem-solving efforts. There are three basic ones, though, that are more common than the rest. Fortunately, these are also relatively easy to solve.
- People treat symptoms. Focusing on symptoms is the Band-Aid approach. In most cases when this is done, the problem will simply pop out sideways. A better approach is to go after the root cause and solve the problem once and for all.
- People don’t set clear goals. If you don’t have a target, it is impossible to know whether you solved the problem. You can make progress without a clear goal, but you’ll never know if you’ve made enough progress to get where you want to go.
- People act without consensus. Few processes affect only a single person. Making changes requires buy-in. When a person solves problems in their head, it is much harder to convince others that the approach is correct.
Why Use a Structured Problem-Solving Approach?
Structured problem-solving helps address the most common failure modes. The first thing it does is helps to prevent errors. People are less likely to skip important steps or make other procedural mistakes when they are following a process.
That process also helps with communication and teamwork. Because a structured problem-solving approach, such as the PDCA process, is widely known, others can catch up very quickly. You don’t have to explain your process for problem-solving to people. You simply have to show what you did. Not only does this speed the communication and coordination time, but it also instills a much higher level of confidence in others.
Using a structured approach also helps improve the problem-solving process itself. Without a standard approach, it is very challenging to get better at problem-solving. Using a method provides a basis for improvement.
Closely related to improving the process is improving one’s ability to follow the process. Structured approaches like PDCA lets a mentor be more effective in guiding a student. The framework lets them focus on the student’s thought process about the problem, rather than about the approach the student is taking.
History of the PDCA Cycle
- Edwards Deming was a quality guru who was instrumental in laying the foundation for recovery in post-World War II Japan. He is also widely considered to be the creator of the PDCA cycle. In fact, this methodology is often called the Deming cycle.
The truth though, is that Deming did not create this process on his own. He based his cycle on an idea of Walter Shewhart. Shewhart, though presented his original cycle as “Plan-Do-Observe-Study.”
Deming’s method was taught to Japanese companies, one of which was Toyota. Eventually Toyota’s success led to a great deal of study of its methods, which brought the PDCA cycle into global prominence.
Incidentally, there are stories that later in life Deming claimed that PDCA actually came from a translation error. He preferred PDSA, meaning “Plan-Do-Study-Act” or “Plan-Do-Study-Adjust”. The issue was that “check” was much more cursory than “study” and did not promote as deep of an understanding of the problem.
Alternative Problem-Solving Methodologies
The PDCA cycle is not the only problem-solving methodology in common use in the continuous improvement world. DMAIC (define, measure, analyze, improve, control) is a structure used in Six Sigma. “8D” or the “8 Disciplines” is another commonly used problem-solving method. Even the basic process of a kaizen event promotes structured problem-solving.
The truth is there is a great deal of overlap in these methods. While each might be most suitable to a specific situation, using any of them will greatly improve your ability to get effective solutions.
When to Use the PDCA Cycle
The PDCA cycle should be used whenever there is a change in a process. These changes come from a few basic reasons.
- An issue is identified and needs to be resolved.
- An opportunity or need for improvement presents itself.
- An external change, such as a regulatory requirement demands a new process.
Notice that each of these things is closely related to the definition of problem presented earlier. All three of these reasons create a change in the gap.
The “Plan” Step
The plan step lays the foundation for the entire problem-solving effort. It involves quite a few items.
- Identify the problem
- Define the problem
- Do you need a stopgap?
- Set SMART goals
- Collect data
- Determine the root cause
- Make a plan
- Predict the outcome
The last item on this list is one of the most frequently overlooked. It is closely related to the hypothesis step of the scientific method. If you cannot properly predict the outcome of your changes, you most likely do not fully understand the root cause.
The “Do” Step
The “Do” step is more than just completing a list of action items.
- Experiment
- Pilot, if needed
- Implement changes
Experimentation should be a big part of this phase of your problem-solving. If you already knew how to correct things, there is a good chance you would have already done it. Often you start this step with only a basic idea of what you want to try. You’ll need to play around with the concept before you get it right.
The “Check” Step
The “check” step should more accurately be described as “study.” The major focus should be on learning about the process. You should also be looking at whether your prediction was on track or not. If it was not, make sure you understand why.
Of course, you do want to check to make sure that the problem was actually improved.
The “Act” Step
Regardless of the outcome of the previous step, you have to take action. If you did not get things right, you have to go back to an earlier part of the PDCA cycle and try again.
If you got things correct, though, your work is still not done. You have to fully implement the change, document the new process, train your team, and communicate the changes to all the stakeholders.
The PDSA Cycle (Plan-Do-Study-Adjust)
As mentioned earlier, Deming actually preferred PDSA. There is also a consistent rumble of people who push for this alternative.
The truth though, is that PDCA is far too entrenched for it to be supplanted by PDSA. That does not mean that the reason for the drive to change it is flawed. A deep emphasis on studying the process can still be put in place, regardless of whether you call it PDCA or PDSA. There is nothing that prevents you from making sure that problem solvers have a deep understanding of how a process works, both before and after changes.
PDCA Cycle Warnings
- Resist the urge to skip steps, especially while you are inexperienced with PDCA.
- Make sure you have a good understanding of the root cause before making any changes.
- Be specific about your goals. That means deadlines and specific numerical targets.
- Don’t skimp on the planning time. People tend to have the urge to rush into making changes.
Using a problem-solving methodology gives you credibility with your leaders. When you simply tell them about a change you would like to make, or a problem you’re having, your information can get lost in the noise. Managers are extremely busy. The better you can package something for them, the more likely they are to use the information.
The PDCA cycle is something that helps your manager quickly fathom what you are trying to tell them. It saves them time and shows your commitment to solving the problem. Both of those make it more likely that you will get the assistance you need.
A further benefit of learning a structured problem-solving methodology is that it will separate you from those around you. Most people do not follow a process when solving problems. As a result, they tend to face the same issues over and over. When you are more effective at getting things done right the first time, your list of accomplishments tends to be longer. That can be a differentiator when promotion time comes around.
The PDCA cycle gives you an outstanding opportunity to mentor your team. You don’t get to just see the results of what they are doing. You also get insight into how they think. That knowledge will help you focus your coaching effort. You can try to cultivate their strength and address their weaknesses in a more effective manner.
In addition, using structured problem-solving conserves your resources. You should only be spending you and your team’s limited time and effort on a particular problem one time. Far too often a problem comes back over and over. Not only is this wasteful, but it also hurts morale.
A big benefit of PDCA is that it allows you to delegate tasks and be able to follow progress better. The problem for managers, especially inexperienced ones, is that they can have trouble letting go of the controls. When you understand how your team will approach a task, it is far easier to give them latitude.
Key Points to Using the PDCA Cycle Effectively
- The PDCA cycle is a structured approach to closing the gap between the current situation and the target condition.
- Structured problem-solving not only helps prevent mistakes, it also acts as a great communication tool.
- Managers have more confidence in their team when they know the PDCA cycle is being used. That means they will be more willing to delegate and will grant more authority for teams to make changes on their own.
Identify a basic problem in your work area and apply PDCA to it. This will work best if you find a mentor who has experience with this problem-solving technique.
Several forms make use of the PDCA cycle to perform a specific function. These include
- The A3 Report: This form is the communication tool associated with A3 Thinking. It is used for complicated, team-oriented problems and is highly conducive to mentoring.
- The Countermeasure Sheet: This form is primarily used to get KPIs back on track.
- The Kaizen Charter: While this form primarily supports the “plan” step of the Deming cycle, it paves the way for using PDCA in a kaizen event.
- Daily Management Worksheet: This form is useful for managing operations with several people doing similar jobs. It is a variation of a shop floor management process that is adjusted for use in office environments.
We’ve got a bonus audio track for you. It is set up on YouTube for your convenience.
3 Comments
Imran · November 4, 2011 at 8:02 am
Oh, thank you sir, you solve my problem and help me to make an assignment. Thank you again!!!
mohankumar · May 8, 2011 at 11:10 pm
its very useful for prepare my university exam thank you sir
Kampechara Puriparinya · December 27, 2011 at 1:37 pm
A great initiative of PDCA/PDSA Cycle. It’s
useful for operational plan.