Podcast: The Differences Between Lean on the Shop Floor and In the Office
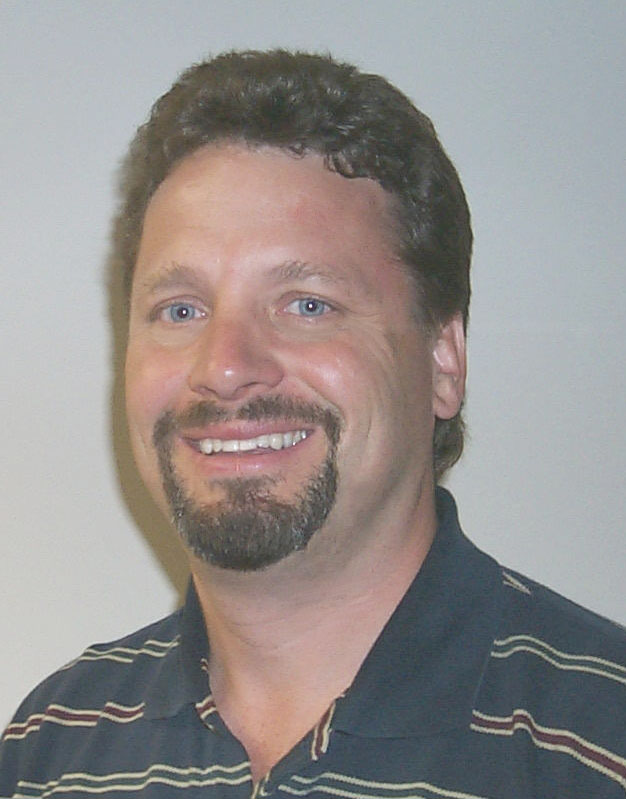
Mike Osterling
We’ve got a special treat for today’s podcast. A few weeks back, I had a chance to interview Mike Osterling. He’s one of the co-authors of The Kaizen Event Planner: Achieving Rapid Improvement in Office, Service and Technical Environments, owns his own consulting business, is a frequent speaker at organizations such as AME, ASQ, and APICS. He also helped co-develop the Lean Enterprise Certificate Program at San Diego State University in 1999.
In this 23 minute MP3 audio presentation, we talk about how Lean in the office differs from its implementation on the shop floor. We discuss how to manage changes, the difference in ownership of jobs, how to recognize abnormal conditions, and what to do to manage the pace of work.
I’m going to apologize in advance for the sound quality on my side of the discussion. It is a little tinny. There’s only so much you can do to clean up the problems with a poor recording. I’ve corrected the problem, so the next one will sound better. But since Mike sounds good, and he does the lion’s share of the talking, I’ll go ahead and post it. Plus it’s free, so If you aren’t satisfied, I’ll give you your money back.
By the way, my next interview is already recorded. It is an interview with Tim McMahon, a Lean blogger, on Lean leadership. Make sure to sign up to receive my blog so you don’t miss it!
0 Comments