Poka Yoke Infographic
Passing on poor quality is a big no-no in a Lean operation. It is disruptive to flow when defects are found far downstream from where the error took place.
Poka yokes support this principle in two ways. The first is that they help to eliminate defects at the source. This is the optimum situation in which a defect never happens in the first place.
The image below shows the second situation where a mistake proofing device can help. In the top example, a typical quality control effort is shown. Inspections are done at the end of the line. If a defect is identified, it is returned to the original station, sent to a rework area, or scrapped. Each of those has a substantial cost associated with it.
The bottom graphic, however, shows what happens when a poka yoke device identifies a defect from the previous station. Because the problem is caught early, no additional work is layered on top of the problem. It can be sent back to the original station quickly while the issue is still fresh in the operator’s mind. That helps with creating a permanent countermeasure. It also helps create ownership of quality issues. Operators know that if they pass on poor quality, they will be asked to help fix it in a matter of moments.
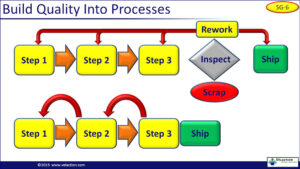
Build Quality Into Your Processes
0 Comments