Work Lean: Ride the Continuous Improvement Wave
How do you work Lean? It means dedicating a part of your time to continuous improvement. Many people say continuous improvement is important, but then don’t treat it like an actual part of one’s job.
But when you work Lean efforts into a schedule, you are making a statement that it is not an afterthought. When a leader staffs her team with enough time to work on Lean projects, she is showing her commitment. If continuous improvement has to be squeezed into a work day, Lean will not blossom like it should.
Think of it this way. If projects aren’t accounted for in the staffing plan for a ten person team, and each person is on a kaizen project twice a year, that’s twenty weeks of being short handed. Not exactly the right way to make a team see a benefit to being on a project.
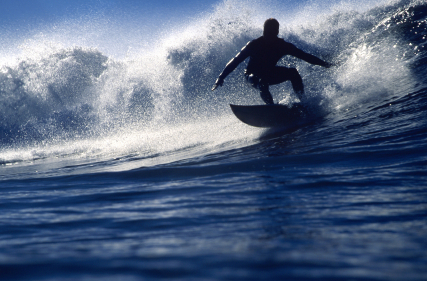
I call building improvement time into schedules ‘riding the continuous improvement wave’. It’s like surfing. Get out in front of the wave, and it is easy to get to shore. If you are behind it, you have to paddle furiously to make headway. When you have the resources available to work on Lean projects, progress comes easy. When you are scrambling to fill teams with people who are focused on the work piling up on their desks, making improvements is considerably harder.
The long term benefit of staffing to work on Lean efforts, though, is that resources are freed up at an increasing rate. Try this with the next 5% of your team (or time) that you free up with continuous improvement. Designate them as continuous improvement staff instead of assigning them to another production process. You might even form them into a resource team to support the rest of the organization.
Great Lean companies commit to working Lean—not just in heart, but also by treating improvement efforts as part of the job and staffing for it.
0 Comments